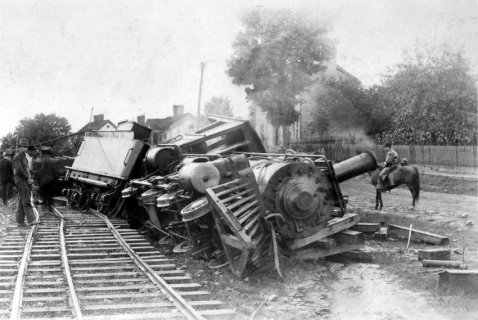
Universal Black Oxide
Sprockets, universal joints, and PT components take on a protective and attractive black oxide finish when treated with TRU TEMP® low temperature, non-polluting black oxide.
Eden Prairie, Minnesota: In-house black oxide finishing for gears is becoming more attractive than outsourcing for one simple reason: it offers more effective control of quality, scheduling and costs. This article describes the latest trends in black oxide finishing and offers an in-house alternative that enhances quality, speeds shipments and lowers costs. The True Cost Of Outsourced Black Oxide Finishing Due to the hazardous nature of most black oxide processes, manufacturers have traditionally been forced to ship parts to an outside plant for black oxide finishing. In the process, they incur extra costs and turnaround times that make it difficult to satisfy customer shipping demands. In addition, this outsourcing requires higher in-process inventory levels and makes it impossible to have direct control over quality. By contrast, in-house finishing streamlines workflow and lowers inventory levels, thereby freeing up cash for other uses. An automated in-house black oxide process line allows the manufacturer to machine gear components, black oxide finish quantities the same day, then immediately proceed to assembly or shipping, without delay. It allows the manufacturer to focus on fabricating components (the highest value contribution), then quickly and efficiently handle the black oxide finishing (the lowest value contribution), without disrupting the smooth flow of components through assembly, packaging and shipping. Automated low temperature black oxide finishing is user proven to be an effective control of quality, scheduling and costs when done in-house. Why Blacken? Black Oxide Is Often The Most Desirable Finishing Option Black oxide adds value and sales appeal to gear and power transmission components, without altering dimensions or interfering with part assembly or operation. In addition, black oxide finishes are quite durable and offer long-term corrosion resistance in storage or in service. In-house black oxide enhances ISO and “Lean Manufacturing” programs because inventory stays in the plant. Black oxide, particularly the low temperature process, is supplied in a variety of pre-engineered systems, complete with operator training, as described below. Making The Right Black Oxide Process Choice With three types of blackening in common use, it’s important to weigh the benefits of each before choosing one for an in-house installation. The first is traditional caustic black oxidizing which utilizes a boiling caustic soda bath operating at 290°F. This system forms a black iron magnetite finish in 20 to 30 minutes. Overall finish quality is usually good, except on cast iron or MIM parts (red coatings are common) or parts with blind holes or recesses (white salt leaching occurs). |
You might also like
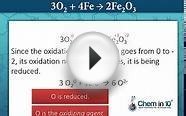
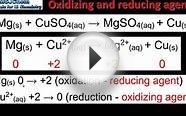

11 Piece Adjustable Wrench Set, 8" Adjustable Wrench, Reversible, Movable Jaw with Serrations, Fits 6 Fastener Types, Includes 10 Universal Sockets, Corrosion Resistant Black-Oxide Finish. Home Improvement (Crescent)
|
![]() |
Craftsman 19 Pc. Universal 1/4-in. Dr. Socket Wrench Set Home Improvement (Craftsman)
|


![]() |
Armstrong 20-520 1/2-Inch Drive 12 Point Black Oxide Universal Socket, 5/8-Inch Home Improvement (Armstrong)
|
![]() |
Stanley Proto J5270AB Drive Oxide Universal Joint, 3/8-Inch, Black Home Improvement (Anchor Fasteners)
|
![]() |
Craftsman 7-Piece Metric Universal Ratcheting Wrench Set # 21030 Home Improvement (Craftsman)
|