Black Oxide Finishing
Last name is required!
First name is not valid!
Last name is not valid!
This is not an email address!
Email address is required!
This email is already registered!
Password is required!
Enter a valid password!
Please enter 6 or more characters!
Please enter 16 or less characters!
Passwords are not same!
Terms and Conditions are required!
Email or Password is wrong!
This new technique was developed by the commercial gun blue manufacturers as a more environmentally friendly system than the commonly used hot application. Parts requiring blackening are simply placed in the liquid at room temperature, no electrical power is required.
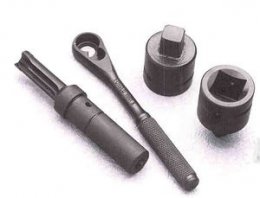
Convenient - Easy to do in house. No waiting for heatup of blackening solution. No waiting for the unpredictable return of parts from an outside vendor. Eliminates high outside vendor costs. Retain control of production and quality. Ideal for high volume or short runs. Works especially well for blackening large volume of small parts in a rotating barrel.
Higher Productivity - Parts can be blackened in two minutes vs 15 to 30 minutes for hot oxide. Normally twice the amount of parts can be blackened in the same amount of time as with hot oxide.
Controllable - Long bath life, blackening solution may be replenished indefinitely with periodic additions of fresh concentrate.
So easy to install and use that you can now economically apply a pleasing decorative, sales-appealing black corrosion-resistant finish on parts previously left unfinished.
Versatility - Blackens cast iron, forged steels, mild steels, hardened tool steels and powdered metal parts. No white salt bleedout as is common with hot oxide.
Dimensional Control - No heat distortion. No smutty rub-off as with other room-temperature blackening processes.
Energy Cost Saving - Blackening is done at room temperature vs hot oxide blackening done at 290°F.
Safety - Blackening solution uses odorless, mild water-dilutable chemicals that require no venting vs hot oxide. No hazardous caustic chemicals with fumes that present health hazards and no spattering of hot, skin-burning chemicals.
Low Maintenance - Longer Equipment Life - No expensive pollution control equipment.
Parts Coverage - 600 to 1200 sq. ft. of surface area blackened per gallon of concentrate.
How to achieve professional results in minutes:- Thoroughly clean the part to be blackened by either sandblasting, wire brushing, wire wool abrasive cleaning, or by scrubbing in 'VIM' or 'COMET' household abrasive cleaner. Make sure you have removed all rust, paint, oil and grease.
Immerse the part in the mixed Black Oxide Solution and swirl around for between 30 seconds and 5 minutes. Alternatively, the part may simply be placed in the solution for 5 - 10 minutes. Remove the part from the solution and rinse in fresh water.
You might also like
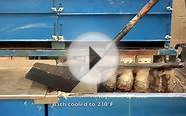
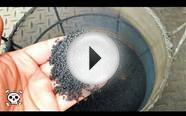
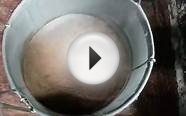
![]() |
Black & Decker 74-586H Assorted Finishing/Detail Sandpaper with Tips, 5-Pack Home Improvement (Black & Decker)
|
![]() |
DrillSpot #8 Black Oxide Finish Countersunk Finishing Washer, Pack of 10000 Home Improvement (DrillSpot)
|